In an electric vehicle, there are 3 main constituent elements or systems:
- An energy source.
- A propulsion system.
- An auxiliary system.
In this post, we will talk about one of the important elements of the propulsion system, namely traction motors. We will consider their types and features of operation. We will also consider the specifics of the electric motor in hybrid cars. Of course, we will talk about the principle of operation of the electric motor.
The information is very important and interesting. So make yourself comfortable and be very careful. Let’s start!
The electric motor-generator
The propulsion system is the heart of the electric vehicle, and the electric motor is located right in the center of the system. The electric motor converts electrical energy from the battery into mechanical energy, which allows the vehicle to move. It also works as a generator during regenerative braking which sends energy back to the source.
But not everything is as simple as it seems. An electric motor is extremely efficient. Only 5% of the energy is lost. You should agree that this power must be curbed, and you should be able to handle it. for this, you need to know some peculiarities of the work and the types of electric motors.
ICE engine vs Electric motor
Torque and power
If we compare electric motors with internal combustion engines, we immediately need to note a number of their significant advantages
- An internal combustion engine consists of much more moving parts than an electric motor. This directly indicates the high reliability of an electric motor in comparison with the internal combustion engine.
- The engine torque reaches its maximum immediately when it is turned on, thus, electric cars do not require the presence of starters and gearboxes typical for ICE.
Speed range
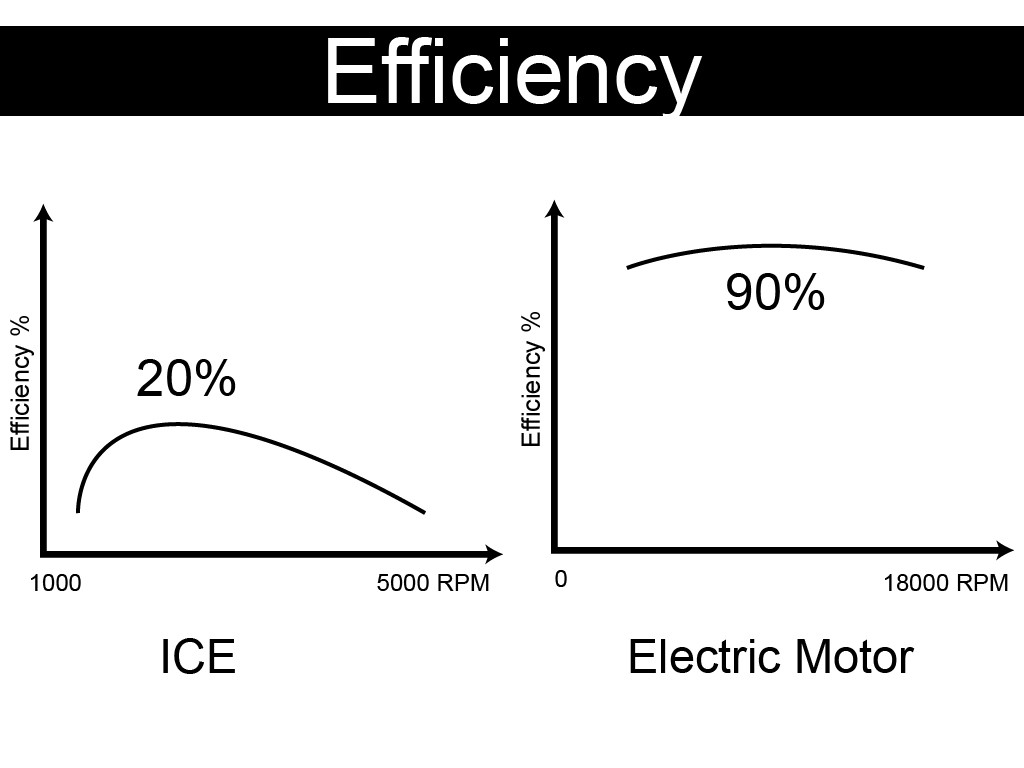
The operation of the electric motor at different speeds from 0 to 18000 RPM with high efficiency allows the electric car to do without a gearbox. To reverse the engine that is to turn on the reverse it is enough to change the polarity for DC motors, or phase rotation for AC motors.
Specific parameters
The specific energy parameters of the electric motor are much higher than that of the internal combustion engine.
Example: Typical ICE vs Tesla induction motor
Parameters | Typical ICE | Tesla induction motor |
---|---|---|
Weight | ≈ 180 kg | 31.8 kg |
Power | ≈ 140 kW | 270 kW |
Weight/Power | ≈ 0.8 kW/kg | 8.5 kW/kg |
However, it is necessary to understand that it is not safe to start an electric vehicle from the entire potential of torque, which is much more powerful than many cars with internal combustion engines, and this causes inefficient battery consumption.
Types of electric motors that used in EVs:
- DC motors.
- AC motors.
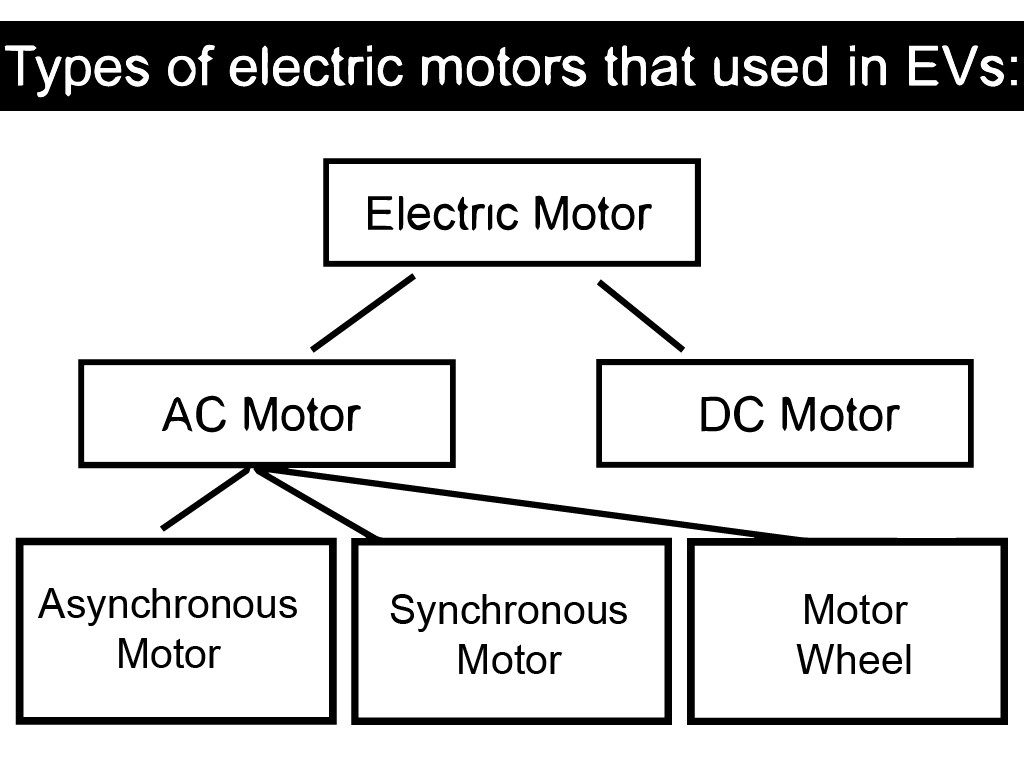
Direct current (DC) motors were used in the first models of electric vehicles. Then, alternating current (AC) motors – asynchronous motors began to gain increasing popularity in the field of electric vehicles. This happened due to several advantages of asynchronous motors, such as:
- The best indicators of specific power.
- Higher efficiency lower weight and dimensions.
- The absence of a brush-collector unit.
The emergence of reliable thyristor and transistor converters contributed especially to this. All this explains that in modern electric vehicles, alternating current (AC) electric motors are mostly used.
AC motors can be divided into three types:
- Asynchronous motors.
- Synchronous motors.
- Motor-wheels.
Asynchronous electric motors (Induction motors)
Let’s begin with asynchronous motors. Their speed of rotation of the rotor is different from the speed of rotation of the magnetic field of the stator or synchronous angular velocity of the motor. It lags by the value that is called a “slip“.
According to the number of phases, there are 3 types of asynchronous electric motors:
- One-phase electric motor.
- Two-phase electric motor.
- Three-phase electric motor.
Principle of operation of an electric motor
Let’s consider the principle of operation of an electric motor on the example of an asynchronous three-phase electric motor since such motors are used as traction motors in electric vehicles.
As was mentioned earlier, a three-phase electric motor is powered by a three-phase alternating current (AC). The stationary part of the machine is called the “stator“. the movable part is the “rotor“.
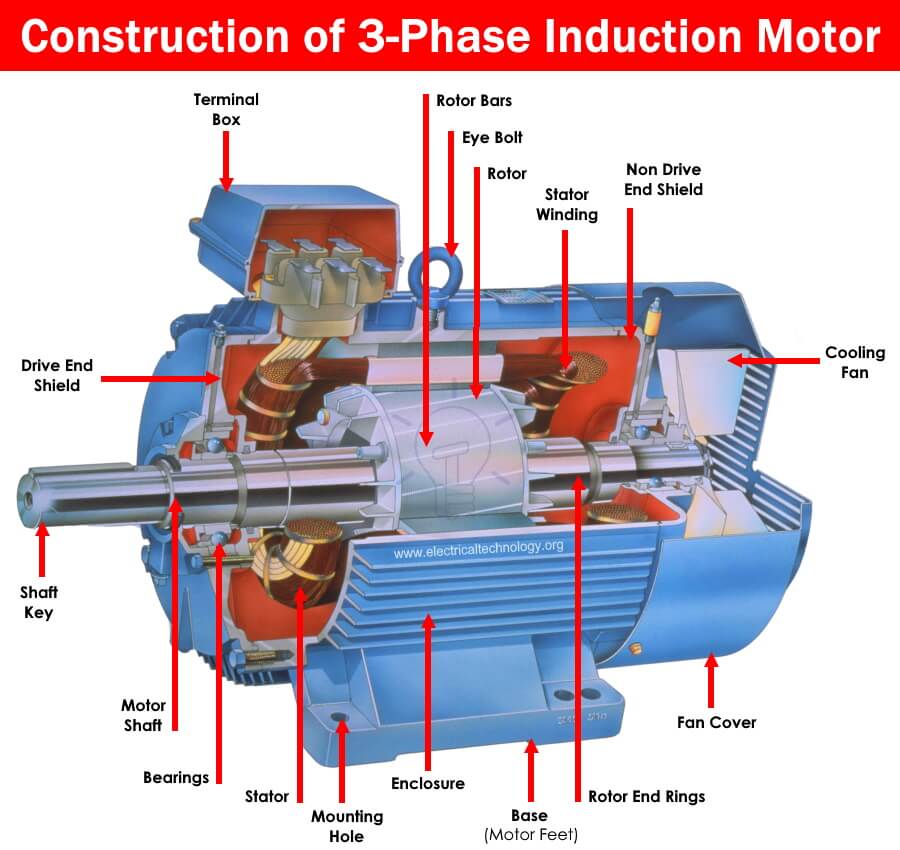
The stator and rotor cores of asynchronous machines are assembled (mixed) from individual electrical steel sheets. On the inner surface of the stator and the outer surface of the rotor, there are grooves in which the winding conductors are placed.
Primary winding
The stator winding is three-phase, connected to the three-phase current network, and is called the “primary winding“.
The rotor winding can be made three-phase similar to the stator winding. The end of the phase of such a winding of the rotor is usually connected to a “star”, or else may be in a “triangle“. and the beginning is brought out to the outside, utilizing slip rings and a metal graphite brush. Such an asynchronous machine is called a “phase-wound rotor machine“.
A three-phase starting or adjusting rheostat is usually attached to the contact rings. The phase winding of the rotor is performed with the same number of poles as the stator winding.
Squirrel cage winding
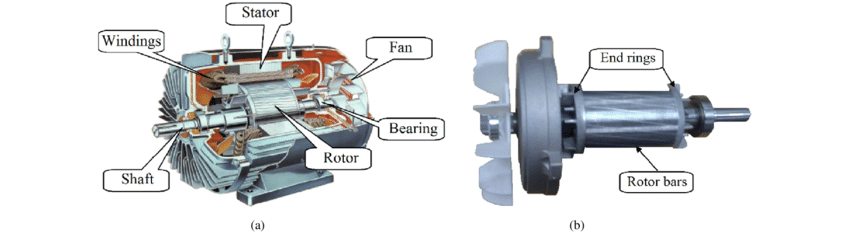
Another type of rotor winding is a “squirrel cage winding“. The ends of the rods of such a winding from both ends are short-circuited by rings, so the winding does not have any leads. Such an asynchronous machine is called a “squirrel cage machine“.
In machines up to 100 kW, the rotor winding is made by casting with aluminum. In larger machines, copper welded winding is used. The absence of a sliding contact on the rotor ensures high reliability of operation of such an engine, and the simplicity of the manufacturing technology ensures the low cost.
For these reasons, asynchronous motors with a squirrel cage rotor are widely used in various industries, including transport.
The principle of operation of the asynchronous motor
The stator winding, when powered by its three-phase current with frequency, f1 creates a rotating magnetic flow with rotation frequency n1. where p is the number of pairs of poles of the stator winding. The frequency of rotation of the magnetic field n1 is called “synchronous rotating magnetic flow”. F1 induces EMF in the rotor winding. Since the rotor winding is closed a system of rotor currents appears and a rotating flow of the rotor F2 is created.
As a result of the interaction of stationary relative to each other flows of the stator and the rotor, the resulting flow F is formed. The interaction of the F and the rotor current causes the appearance of electromagnetic forces and electromagnetic moment.
In the engine mode, under the action of this moment, the rotor rotates in the direction of rotation of the magnetic field.
In the generator mode, for example, when braking an electric vehicle the rotor rotates with a drive motor at a speed of n> n1 and the EMF of the stator winding exceed the mains voltage and the machine sends energy to the network that is starts charging the traction battery.
The frequency of rotation n of the rotor of the asynchronous machine is always different from the frequency of rotation of the magnetic field n1 which is called synchronous. It is the reason for the machine name – asynchronous that is not synchronous, in which n ≠ n1.
Synchronous electric motors
Such electric motors also operate on alternating current. But, unlike asynchronous, their rotor motion is completely symmetrical to the electromagnetic field. Similar electric motors are used at high power.
The stator of a synchronous motor is called an “anchor“. There is a three-phase winding on the stator uniformly distributed along with the slots armature winding. The number of poles of the stator winding is equal to the number of poles of the rotor. The rotor is called an “inductor“. and has an excitation winding fed by a direct current. The current is supplied through two contact rings and brushes.
Low power motors can be excited by permanent magnets. According to the rotor design, the salient pole and nonsalient pole synchronous motors have distinguished.
The advantage of synchronous motors compared to asynchronous motors is the ability to precisely adjust the electric motor for use in the car. Also, the synchronous motors have a higher power factor and therefore higher efficiency. which is 0.5-3% higher than that of asynchronous motors.
Motor Wheel
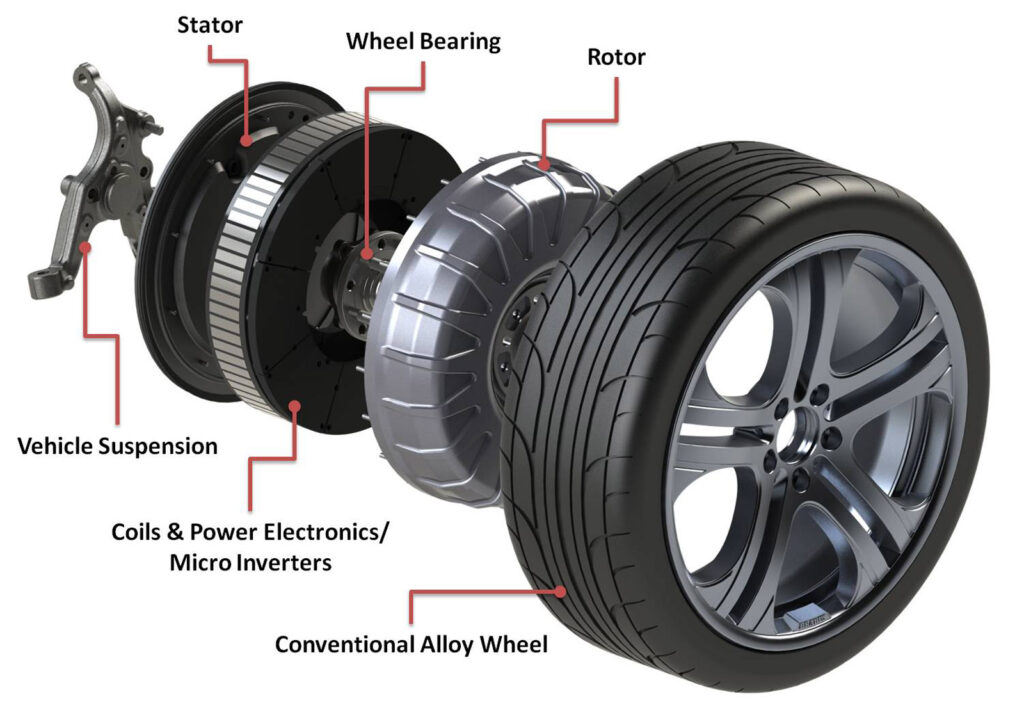
In this type of engine, voltage, and torque is designed for a specific wheel. Motor-wheel is often used in plug-in hybrid cars in a working tandem with the ICE engine. The motor-wheel is a contactless electric motor in which the stator rotates, not the rotor. The stator is also a wheel rim.
The distinctive features of a motor-wheel:
- A gearless electric motor built into the wheel hub.
- High-coercive permanent magnets based on liquid metals.
- High torque-weight ratio and
- The use of composite materials and alloys
The advantages of a motor-wheel:
- The absence of a gearbox block causes high reliability and consequently, a longer service life.
- The controlled speed of rotation of the motor-wheels is achieved using the control system.
- Increased smoothness of run because the absence of a gearbox allows the engine to rotate with very high accuracy.
- This electric drive has almost absolutely silent operation due to the use of new materials.
The design of the motor-wheel makes it possible to install it directly into the wheel. But in modern electric vehicles, they deviate from such an arrangement of the motor. Because installing the motor-wheel directly into the wheel increases the chassis specific gravity, increases the springless masses of the car, and reduces its controllability.
Also, bad roads contribute to the destruction of both the permanent magnets on the stator and the suspension elements of the car which has a lot of weight compared to a conventional design.
Using an electric motor instead of a motor-wheel as a full drive for rotating a wheel is more rational. Although, in some designs of electric vehicles the use of motor-wheels is justified. For example, segway, monowheel, electric bicycles, etc.
Hybrid cars have their specific use of electric motors. The hybrid motor acts as an auxiliary element. It increases the power of the main internal combustion engine and reduces fuel consumption.
Types of electric motors that are used in hybrids
Let’s look at some types of “functions” of electric motors that are used in hybrids.
- Built-in motor assistance: The electric motor takes over the part of the effort to create torque while driving
- Built-in starter generator: In this case, the electric motor only sets the car in motion.
- Start/stop engine: The system of the electric motor, which turns off the main ICE engine when stopped and instantly starts it at the beginning of the movement.
Summary
We have got onto how electric motors are classified, their features of operation, advantages, and disadvantages. We inquired into the principle of operation on the example of an asynchronous three-phase motor. We also reviewed the specifics of the motor in tandem with the internal combustion engine in hybrids.
We hope this article was very informative and that everything was as simple and clear as possible. In case you have any questions, you can ask them in the comment section below. See you in another article!
You may also like to read: Electric Car Motor Lifespan – How long does an Electric Car Motor last